Staroxy SL 500
Food Grade Self Leveling Epoxy Floor Coating
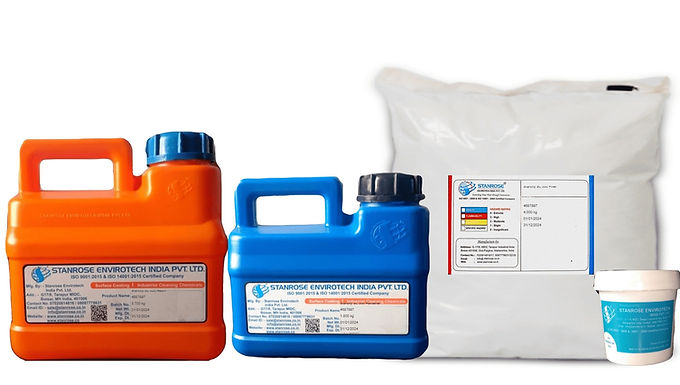
Description
Staroxy SL 500 is a pigmented, solvent-free, high- build epoxy floor coating system designed to offer seamless, durable floor protection at applied thicknesses between 0.3 to 0.5 mm.
With the addition of Stanrose Aggregate between coats, anti-slip resistant applications can be achieved in system build-up thicknesses between 0.50 to 2.0mm.
Available as a 4-part component kit.
Staroxy SL 500 exhibits excellent wear, abrasion and chemical resistance and is suitable for use in a wide variety of industrial and commercial applications. It can be used to provide a surface coating with a high gloss hygienic finish or a slip resistant coating system.
Staroxy SL 500 provides impermeable protection against common oils, greases, lubricants, aviation fuels and hydraulic oils such as Skydrol. As in all corrosive situations, a full analysis of operating and exposure conditions is required, followed by reference to chemical resistance data to ensure product suitability.
Staroxy SL 500 has been certified by CSIR – Central Food Technological Research Institute, Mysore (CFTRI) against USFDA 175.300 1st April 2018, for intended use for contact with aqueous (water) food/beverages at room temperature filling and storing.
Uses
Staroxy SL 500 can be used extensively in, but is not limited to the following areas of application:
• Chemical manufacturing plants.
• Pharmaceutical and other medical facilities.
• Car production and showroom facilities.
• Aircraft hangers and maintenance areas.
• Warehouses with high density traffic.
• Food and beverage production areas.
• Vehicle movement areas.
Advantages
• Simple application.
• Excellent anchoring to the surface
• Provides high tensile and impact strength.
• Excellent wear and abrasion resistance.
• Superior chemical resistance.
• Smooth high gloss finish for hygienic applications.
• Slip resistant finish in trafficable applications.
• Easy application by brush, roller or squeegee.
Technical Properties
• Generic Type: Amine based Epoxy
• Dry Time:
o To Touch – 8 Hrs.
o To Recoat – 14 Hrs.
o Foot Traffic – 14 Hrs.
o Full Cure – 7 Days
• Pot Life: 30 Minutes
• All data is valid for mixed material.
• Volume Solids (ASTM D 2697): 100%
• Flexural Strength: > 40 N/mm2
• Tensile Strength: > 20 N/mm2
• Bond Strength: Greater than cohesive strength of quality
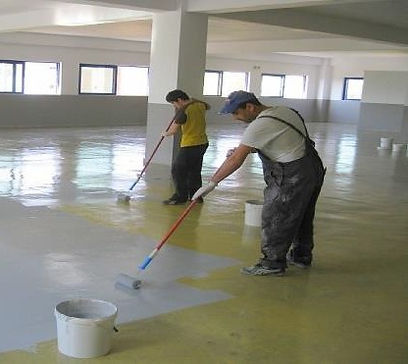
Directions for Use
Substrate Requirements:
• To secure lasting adhesion to the subsequent product all surfaces shall be clean, dry and free from any contamination. Substrates Temperatures must be a minimum of 55-60°F. and a maximum of 85°F.
• Laitance deposits are best removed by Planetary diamond disc grinder or by captive blasting followed by vacuum cleaning to remove dust debris.
• Substrate must be clean and free of Dirt, waxes, curing agents and any other foreign material that will interfere with bonding.
Surface preparation:
Remove oil, grease and any other contaminants using thinner. Blast clean to minimum Sa 2½ (Swedish standard SIS 05 5900). If blasting is not practically possible, make full use of mechanical tools to remove loose rust and scale to St.2 Swedish standard. Surface should be clean and dry before application of Staroxy 103 MOT Primer. New concrete or cementitious substrates should have been placed at least 28 days and have a moisture content of less than 5% before topping with Staroxy 103 MOT Primer.
After surface is dry, all repair work like sealing of joints, crack filling of cavities and crevices should be carried out.
If the surface is Tremix or smooth surface then Shot Blasting is carried out to make the surface rough in order to enhance the bonding of the primer.
Concrete defects such as voids, bug holes, excess porosity, and physical and chemical damage are usually filled or repaired prior to the installation of the F/C system. (Materials such as slurries, mortars, and polymer concrete are used to level, smooth and patch concrete surfaces.
The laitance (A thin, weak, brittle layer of cement and aggregate on concrete surface) on in-situ bases and any surface sealer or curing membrane should be entirely removed by suitable mechanized equipment, e.g. shot- blasting, panning or grinding, to expose cleanly the coarse aggregate
Mixing and Application:
1. Pack components are pre-weighed for optimum performance. Never split packs.
2. Stir resin thoroughly and then mix of resin, pigment, filler with hardener by pack. Empty contents of Resin into a mixing container and pre-mix to assure the suspension of solids. Stir resin thoroughly and then mix pre weighed resin with pre weighed hardener by volume, after that mix with the aggregates provided.
3. Add Hardner and continue to mix to a uniform consistency for 1-2 minutes.
4. Mix with slow speed drill or manually depending on the quantity in mixing bucket and helical spinner head for 2 minutes.
5. Spread the mixture on the floor immediately and allow it to dry for 4 hours.
Method of Application
Staroxy SL 500 is a versatile product and can be applied in various application thicknesses from 300 microns to 500 microns per coat giving DFT thickness of 0.3 to 0.5 mm when applied as a single coat system. To achieve a smooth finish at application between 300 microns to 500 microns per coat, a short hair roller or brush is suitable.
For slip resistant finishes or higher strength, apply the base coat first. This coat can then be scattered with Stanrose Aggregate by completely blinding at approximately 0.5-1.0kg/m². Apply aggregate to wet base coat. After initial cure (12 hours at 40°C) the excess aggregate should be removed by brushing or vacuuming.
Alternative textures can be obtained by varying the amount of Stanrose Aggregate broadcast on to the base/sealer coat.
The top coat can now be applied. Depending on the surface profile, type and density of the Stanrose Aggregates used, the top coat may consume more material than the base coat to achieve a fully sealed surface. The top coat must be applied within the maximum over coating time period i.e. 36 hours at 25°C or 24 hours at 40°C.
Prior to application, Staroxy SL 500 should be stored undercover and protected from extremes of temperature in an air-conditioned environment immediately prior to application.
Packaging Size, Storage and Shelf Life
The product should be stored in accordance with national regulations. It should be kept in a cool, well-ventilated area, away from heat, direct sunlight, sparks and children. Handle with care. It has a shelf life of 12 months from the date of manufacturing.
Available in 10 Kg packs and has a maximum shelf life of 12 months in the un-opened containers.